Krone Big Pack Multi-bale
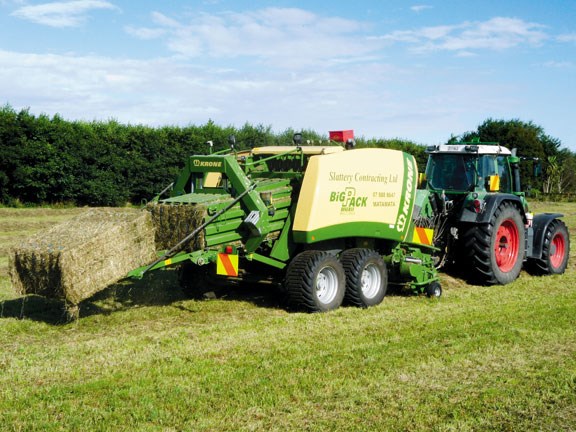
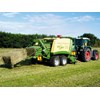
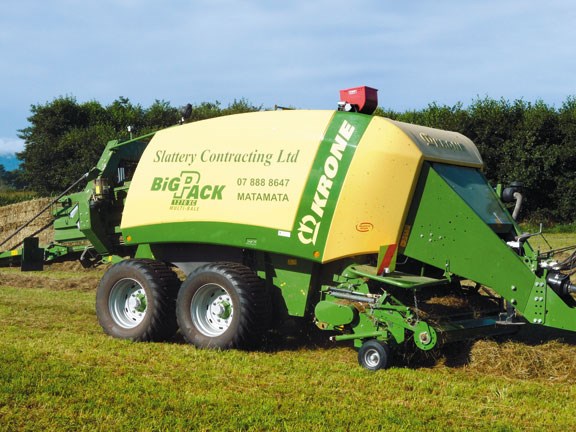
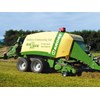
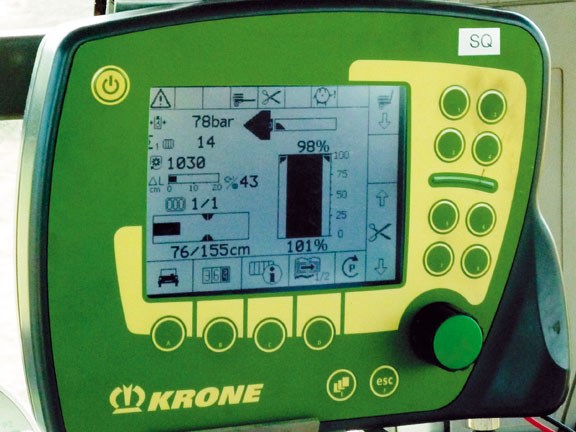
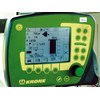
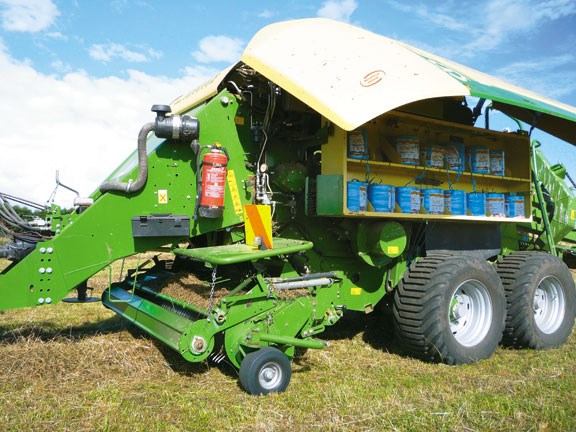
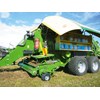
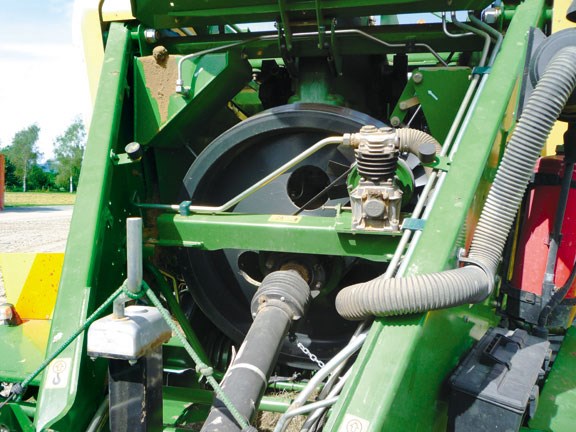
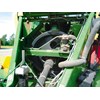
![]() |
![]() |
![]() |
![]() |
![]() |
It was a few years ago at a machinery show that Brent Lilley first saw the Krone Big Pack Multibale. At the time, he thought it had a lot of merit, but was keen to see it working. When the opportunity arose earlier this month to see it in action, he jumped at the chance.
![]() |
Krone Big Pack Multi-bale
|
Unfortunately, plans to check out the baler were put on hold while we waited for a decent break in the weather for hay making, a problem I imagine most have faced this summer.
When I finally did get to Matamata to test the machine, the tedder was just finishing up turning the last paddock of hay and the rake was ready to start rowing up – the perfect timing, as I was able to check out the Krone before baling started.
The Krone Big Pack 1270 XC Multibale was bought in October last year from Piako Tractors in Morrinsville by Roger Slattery, owner of Slattery Contractors. It replaced an older Case LBX baler that Slattery’s team was running.
Slattery says the main reason he chose the Krone was its ability to produce multiple bales, as he sees a lot of potential in their use. The 1200 x 700mm bale size also influenced his decision as it allowed him to transport hay bales stacked four-high on a truck, maximising loads. Slattery adds that he’s been really happy with the support and service he’s received from Piako.
The baler was put to work straight away and has now done over 10,000 bales around Matamata, where Slattery Contracting is based. This season, it’s been pulled by a Fendt 818 and the driver, Jim, says it has performed well in a range of conditions. He has been very impressed with the baler, although initially some things took a little time getting used to.
Pickup
The wide 2.3m pickup on the baler uses five rows of pickup tines, as opposed to four on most other balers, allowing for faster ground speeds when baling while still picking up all the crop. These five rows of tines are cam-less and remain in a fixed position as the pickup rotates. This and the wave-shaped bands on the pickup have the unique effect of feeding in the material evenly against the roller wind guard and throwing it from the back of the pickup into the rotor.
It would be nice to see the bands on the pickup in sections, as I have seen on some other machines, which would enable six or so bands to be removed at once when replacing tines or untangling twine.
The pickup is driven from the side of the main gearbox through to a universal shaft that includes a ratchet overload. The wheels on the pickup are removable to keep the width of the machine down on the road and are adjustable without the need for tools. These wheels are also mounted on a pivot, which allows for some sideways movement when turning with the pick up on the ground. This will cut down on scrubbing and punctures in these tyres.
Knives and rotor
When fitted with the Krone X-Cut system, like this baler has, it uses a large heavy-duty rotor fitted with Hardox plates on the tips to drag the material into the baler and across the knives in a V pattern. The drive for the rotor also comes direct from the main gearbox through a universal shaft and an overload clutch.
The knives themselves have a spring protection system, allowing them to move out of the way of any foreign objects then return to the cutting position. They are arranged in two trays which contain a maximum of 13 knives each, and slide out on either side of the baler for easy access.
The knife control system allows for all, half or none of the knives to be in the cutting position, and with all 26 knives in, the baler has a theoretical chop length of 44mm. The knives are all held on a drop floor that can be hydraulically lowered from the cab to allow blockages though the machine.
Stuffer
The Krone uses a rotating drum stuffer, which is very different from the mechanical arm and cam system that is used on many square balers. This system uses a large continually rotating drum above the feed chamber that contains five packer tines and one feeder rake which run on a cam track. These packer tines drag the material off the back of the rotor, push it up the chamber and pack it against the retainer hook at the top of the chamber.
When the chamber is full, the retainer hook moves out of the way and the feeder rake pushes the material up into the baler chamber. This system gives a consistent flake size every time, regardless of the size and shape of the windrow or speed of the machine. You can see this in the bales the machine produces: they are solid square and uniform length bales with excellent top fill.
The rotating drum stuffer and feed chamber is an excellent system, the only potential problem that I can see is that it’s very hard to access being fully enclosed. If you do manage to block the feed chamber (and I have on other balers in the past), then it is going to be quite some job to get it unblocked.
Baler
The drive for the baler comes from the tractor through a wide-angle double universal PTO shaft and a friction overload clutch to a massive flywheel in the front of the machine, then onto the main gearbox. Krone has used large flywheels in their balers to smooth the drive train load on the tractor, lowering the power requirements. An air compressor is mounted near the flywheel and driven off the power shaft enabling the baler to run its own closed compressed air system.
The Krone runs with a long plunger stroke at 38 strokes/minute. The main gearbox drives the plunger through a heavy set of arms to pack the material being baled into the extremely well-built funnel shaped chamber that helps produce those solid square bales mentioned earlier. The chamber on the baler is kept at the required pressure by the closed onboard hydraulic system powered by a hydraulic pump run off the baler drive shaft.
Hopefully you’re starting to pick up on the trend here: the drive for everything on the baler is through universals, shafts and overrun clutches. This means no chains need oiling and adjusting, no shear bolts breaking and needing replacing all in all leading to a quieter baler with low maintenance costs and more time baling.
The ramp on the back of the baler and the ejectors in the bale chamber can be hydraulically operated with controls conveniently located on the back left hand side of the machine, in addition to this the last bale can be ejected and the ramp raised from the control box in the cab.
Knotters
The six double knotters for the machine are up on top under an easily accessed cover and are the same knotters that are found in many big square bales on the market. They offer great reliability and the double knot that they tie (one knot at the top of each end of the bale), are exceptionally good when it comes to baling tight bales or heavy silage.
The Krone uses the on-board compressed air system to keep the area around the knotters clean, resulting in less missed knots and dropped twines. The electronic star wheel for bale length metering is located on the floor of the chamber and controlled from the cab to give a consistent bale length.
The Knotters along with most things on the baler are kept greased by the electronic auto lube system on the baler and there are only a few grease points on driveshaft’s that need greasing by hand. The drive for the knotters once again comes though a universal shaft and an overrun clutch.
Multibale
Krone’s Multibale design is an interesting one, which allows you, on a six-string baler with Multibale, to bale up to nine 300mm long, two-string bales inside of a regular bale.
On the day I tested the baler, we were baling a 1500mm-long bale as 10 conventional bale equivalent; these had five small bales inside them. The bale is tied with four strings and when these are cut, operators are left with five smaller bales, with two strings that measure 1200mm wide, 700mm high, 300mm in length. These small bales weigh approximately 50-60kg.
The needles on the Krone Big Pack Multibale are arranged on two separate needle carriages and this is where the secret to the Multibale lies. When the baler is set to bale regular bales, the two needle carriages are locked together with a mechanical lock. When the star wheel measures the bale to the correct length, it electronically trips the tie mechanism and all six needles go up though the chamber to feed the knotters with twine and tie the bale.
With the baler set to make multiple bales on the control box in the cab, the star wheel measures the desired length of the multi bales, then a compressed air ram unlocks the mechanical lock on the needle carriages. The first carriage will push just the two needles on it up through the bale chamber as the knotters will only work when they are fed with twin.
Only the second and fifth knotters will tie to make the small bales. This process repeats till the desired overall bale length is reached, then the needle carriages will lock back together and all six needles will be pushed up through the chamber to complete the bale.
The control box
The baler I tested was running off the Krone comfort control box, which is supposedly the more advanced control and is required when the baler is equipped with Muiltibale. This gives good control and displays a lot of information from sensors on the baler.
Being able to control the length of the bale from the cab, or the length and number when baling multi bales, is really helpful. The chamber pressure can also be controlled on a percentage of the load on the baler so there is little need to adjust the pressure when changing crops.
Overall, I found the control box provided a lot of information, but it could be a little confusing with lots of pages and icons to get lost in. There was also a slight delay between pushing a button and what happens on the screen. I found I accidentally pushed the same button twice ending up with a different outcome to what I was intending. The Krone can be specified on the standardised ISOBUS system, which I think would simplify the operation of the baler.
The verdict
The Krone Big Pack, as a regular, big square baler in its own right, is a very impressive machine. A lot of thought has gone into the refinement and improvement of their balers and evidence of this is in the cam-less pickup, the rotating drum stuffer, feed chamber and the large flywheel, among other things. All these attributes make this an exceptional baler at a high speeds, with minimal stoppages due to less maintenance and breakdowns.
I rate the Krone Big Pack baler far above other balers I have used in the past. The only downfall I see is its price, but then you get what you pay for.
The Multibale system, when fitted to the Big Pack baler, opens up a new range of situations where it can be used. Before I checked out the machine, I thought it may be the answer to doing away with the hard labour involved in picking up and stacking conventional bales, but after seeing the multibales first hand - this is not the case. With the multibales weighing around 50 to 60kg or the same as two conventional bales, they are just too heavy to completely replace conventional bales, rather I believe the multibales are a product that will find its uses in farming systems outside of what conventional bales are being used for.
Positives
- Completely closed compressed air and hydraulic system on the baler independent from the tractor
- Large flywheel for lower power requirements
- Drive train on the baler is though drive shafts and clutches to lower maintenance and breakdowns
- Pre-pack chamber for excellent bale density
- Auto lube for the majority of grease points on the machine
- Multibale system offers diversification for the machine and the bales it produces
Negatives
- Access to the stuffer and feed chamber is limited
- The control box can be confusing to begin with, but having an ISOBUS option sorts this out
- The Multibale is a little heavy for moving around by hand. Perhaps in the future Krone will make a baler that produces a 25kg multibale.
For the latest reviews, subscribe to our Farm Trader magazine here.
Keep up to date in the industry by signing up to Farm Trader's free newsletter or liking us on Facebook